隨著半導體技術的迅速發展以及絕緣柵雙極型晶體管(insulated gate bipolar translator,IGBT)模塊的普遍應用,電力電子可靠性要求不斷提高,而過熱失效這一主要失效原因亦成為IGBT器件研制的障礙。為解決這一瓶頸問題,近年來,國內外專家學者們也將關注的焦點放在了IGBT模塊的熱失效分析方面。熱阻這一表征半導體器件熱傳導的參量也成了熱失效問題中的一個熱點。
IGBT熱阻的測試及計算方法常見的有以下幾種,包括熱傳導法、熱敏參數法、物理接觸法、紅外熱成像法、等效熱網絡模型法等。
熱傳導法以IGBT定義式為基礎進行熱阻計算。這種方法具有用直接基于尺寸參數和材料熱特性解算模塊結殼熱阻和能清楚地反映出模塊內各層構造熱阻值等優點,其不足之處在于模塊內各層導熱材料厚度與有效導熱面積近似,且忽略各層材料熱導率隨著溫度和退化程度的變化。
熱敏參數法首先得到溫敏參數,由溫敏參數求得IGBT的結溫,再根據IGBT熱阻的計算式求得其熱阻。該方法優點是不易對器件造成破壞;缺點是引入了較多的測量誤差,殼溫最大值點難以確定,并且該方法需要在IGBT模塊達到熱穩態時才能進行求解。對此也有很多文獻對該方法進行改進。
物理接觸法主要有利用熱電偶和光纖探頭直接測量結溫或者殼溫的。這種方法具有可直接求出測量點在任意時間內的溫度等優點;其不足之處在于一方面損壞了器件,而且所產生的損傷還影響了溫度分布,而另一方面測量點又不一定是溫度最大值的點,這些都會產生誤差。
紅外熱成像法就是利用紅外熱成像系統測溫的方法。它具有測量精度高、探測速度快等優點;不足之處在于費用較高。等效熱網絡模型法采用計算機軟件編程擬合IGBT模塊瞬態熱阻抗曲線獲得其RC熱網絡模型繼而獲得熱阻。這種方法的好處在于計算速度很快;缺點在于隨IGBT模塊不斷劣化,熱網絡模型中阻容參數需不斷修改且工作煩瑣。
根據以上分析可知,傳統的熱阻計算方法在準確性、測量周期或是成本上都有著些許缺陷,因此,本文根據瞬態熱阻抗計算式提出了一種可以在工況條件下快速、準確計算IGBT模塊結殼熱阻的方法。
IGBT模塊快速計算法原理
JESD51—14中定義,在t=0時刻給半導體器件施加1個恒定的熱功率,那么t時刻的瞬態熱阻抗可通過下式計算:
式中:
TJ(t):為t時刻的芯片結溫;
TJ(t=0):為t=0時刻的芯片結溫;
PH:為施加的熱功率。
電熱比擬理論認為熱阻這一材料本身屬性是恒定的。但熱和電也有本質區別,電傳得很快,也就是電場傳得很快,熱傳得比較慢,有遲滯現象。所以以IGBT模塊為例,熱量從芯片上產生、往下轉移的過程當中,t1時刻,熱量的前端剛剛轉移至襯底層(DBC)下表面,則熱量流過物料的熱阻就是結在DBC下表面上的熱阻,根據式(1)求得的ZθJC(t1)即結到DBC底面的熱阻;當t2時刻熱量前端傳遞到銅基板底面時,那么熱量所流經的熱阻則為模塊結殼熱阻,根據式(1)求得的ZθJC(t2)即結殼熱阻。所以通過研究熱量前端傳遞到銅基板底面的時間節點及該時刻的模塊結溫大小,根據熱量的流經熱阻,由式(1)就可求得模塊的結殼熱阻。
為研究熱量向銅基板底面傳遞的時間節點,對某一恒功率載荷作用下IGBT模塊結殼溫度0.02s之前的變化曲線進行了模擬研究,結果如圖1。
由圖1可知,在t0時刻施加恒功率載荷后,芯片溫度迅速上升,在0.02s時刻升高了0.85℃,而殼的溫度升高出現遲滯性,在0.014s才有較為明顯的升高,且溫度變化速率要小于結溫變化速率,在0.02s時殼溫升高了0.003℃左右。為了準確研究模塊熱能傳遞過程,對圖1中的殼溫變化曲線進行局部放大,如圖2所示。
由圖2可知,殼溫在0.003s前不發生變化,也就是說當t=0.003s時,由芯片吸收的熱量剛好傳遞到IGBT模塊基板底面。
為了便于觀察,只對模塊中1組IGBT芯片的剖切面進行仿真,得出IGBT在0.003s時的瞬態縱向分布,如圖3所示。
如圖3所示,熱流從IGBT芯片到銅基板底面是沿著箭頭方向流動。基于此模擬可知0.003s下熱流正好到達銅基板的底側,這也驗證了我們遲滯性理論的正確性。
通過圖1~圖3可知,熱量從芯片傳遞到銅基板底面的時間為0.003s,由于IGBT模塊芯片到銅基板底面的垂直距離為4.75mm,所以可以求得熱量在IGBT模塊中的平均傳播速度為1.58m/s,遠低于電子在金屬導體中的傳播速度,因此熱量的傳遞與電能傳遞相比具有遲滯性。
IGBT快速計算模型建立
根據對式(1)的分析可知,當tp時刻熱量恰好傳遞至模塊銅基板底面時,由式(1)所計算的瞬態熱阻ZθJC(tp)是模塊熱量所流經的熱阻和,即為模塊的結殼熱阻。
從圖1中可以看出,模塊芯片向銅基板底面傳熱所需時間為10-3s量級,很短,所以利用這種方法可以迅速地計算出模塊結殼時的熱阻,不需要等IGBT模塊達到穩態傳熱模式后再測量。故工況條件采用本方法可得到IGBT模塊開機瞬間結殼熱阻。因為模塊在工作前各點溫度與環境溫度相同,所以模塊結殼熱阻的計算方法如下式所示:
其中,tp滿足:
式中:
Ta:為環境溫度;
Tc(t):為t時刻模塊的殼溫;
Tp:為模塊殼溫剛開始升高的時間點。
從上述研究來看,模擬可以簡便地捕捉殼溫開始上升的時間點和相應時刻結溫。但是在實際工況測量中,要得到這個時間節點就必須同時對模塊結殼溫度進行監測,并根據模塊變化曲線對曲線方程進行擬合,找出ΔTc恰好不是零時的tp值。但是建立數學模型、以及求導分析過程煩瑣,而且在底殼溫度測量點的選擇上存在隨機性,從而造成結殼熱阻結果存在誤差。
為了可以準確獲取tp時刻的結溫TJ (tp),需要對IGBT模塊的傳熱過程進一步分析。當給IGBT模塊施加一恒定功率時,熱量由芯片的PN結產生并垂直向下傳遞,當器件的殼溫沒有發生變化之前,通過式(1)求得的瞬態熱阻大小不受模塊外部散熱條件的影響,只與模塊內部散熱性能有關。因此,對于散熱條件不同的IGBT模塊,由于在此時間段,熱量的傳遞路徑完全一致,所以模塊的結溫變化曲線也完全一致。久而久之,因IGBT模塊銅基板底部溫度上升,熱對流將熱量散到環境中去,這時由式(1)得到的瞬態熱阻較大時,會受到模塊外散熱的影響。針對散熱條件的差異,該時刻之后IGBT模塊熱量傳遞路徑發生了變化,結溫曲線發生了分離。兩種不同散熱系數IGBT模塊在加載同一熱載荷下結溫變化曲線如圖4。
由圖4分析知,在tp時刻,熱量剛好由芯片傳遞至模塊銅基板底面;在tp時刻之前兩模塊熱量傳遞路徑及條件完全一致,所以對于不同散熱系數的IGBT模塊結溫在此時間段變化曲線一致;當tp時刻之后,熱從銅基板底面開始散失到周圍環境中,這兩個模塊因使用對流系數不同而改變了熱傳遞條件,結溫升高速率亦隨之變化:對流系數越高的模塊結溫變化率越低,而對流系數越低則結溫變化率越高。
IGBT模塊快速計算仿真研究
為驗證所提方法的準確性,采用有限元仿真進行了實例求解和計算。為了能夠同時對模塊熱阻進行快速地計算,模擬中在同一個工作平臺上建立了兩個完全吻合的IGBT模塊三維模型并且對其設定了不同對流系數來替代實際測量中相繼兩次的測量。具體解題流程如下。
1.在同一工作平臺建立2個完全一致的IGBT模塊3維模型,并進行完全相同的網絡劃分,如圖5所示。
2.銅基板底面的對流系數分別設為50和100,仿真不同散熱條件的模塊傳熱特性。
3.給2個模塊的IGBT芯片均施加功率為50W的熱載荷。
4.通過仿真獲得IGBT模塊的結溫變化曲線如圖6所示
由圖6可知,在t=0.0014s時,2條結溫曲線發生分離,分離時的結溫大小為TJ(0.0014)=33.3℃。
5.經過仿真可知,TJ(0.0014)=33.3℃,Ta=25℃,P=50W,根據式(2),求得IGBT模塊的結殼熱阻RJC=0.166℃/W。
為驗證所提方法的準確性,采用有限元仿真進行了實例求解和計算。為了能夠同時對模塊熱阻進行快速地計算,模擬中在同一個工作平臺上建立了兩個完全吻合的IGBT模塊三維模型并且對其設定了不同對流系數來替代實際測量中相繼兩次的測量。具體解題流程如下。
解算出結殼熱阻達到0.166°C·W-1。對比上述結果證明IGBT模塊快速計算法是可行和正確的。
IGBT模塊快速計算試驗研究
1、快速計算工況條件實現方法
根據以上分析,在實際工況條件下使用該模型計算IGBT模塊結殼熱阻的實現方法為:
在同一坐標系下繪制不同散熱條件下IGBT模塊的結溫變化曲線,2條曲線的分離點對應的時刻即為殼溫剛開始升高的時間點tp, 此時對應的結溫大小即為TJ(tp)。這樣就可以根據式(2)直接計算模塊的結殼熱阻。
在工況條件下通過該方法計算模塊結殼熱阻的具體步驟如下:
1.使IGBT模塊在環境溫度Ta下達到熱穩態,即模塊各節點溫度均為Ta,沒有熱傳遞發生;
2.給IGBT模塊施加一恒定功率P,采集其結溫變化曲線;
3.改變IGBT模塊散熱條件例如:組裝散熱器后改變銅基板和散熱器間導熱硅脂的厚度、未組裝散熱器后施加或者改變風冷后空氣的速度等。再施加恒定功率P并收集其結溫變化曲線;
4.尋找2次采集的結溫變化曲線分離點對應的結溫大小TJ (tp);
5.根據式(2)計算模塊的結殼熱阻。為了使得測試過程更加快捷方便,可以提前測量不同條件下結溫的變化曲線,形成數據庫。
這樣,實際操作時只需測量1次結溫變化曲線,再與數據庫中同條件結溫曲線進行比對即可。
2、快速計算實驗條件實現方法
通過嵌入光纖傳感器可實現對芯片結溫的精確測量,而無需改變模塊本身的傳熱特性,本部分將基于分離點求取結殼熱阻,并在實驗室工況下對模塊結殼熱阻進行了測量。
根據制定的在工況條件下實驗該方法的具體步驟,設計實驗條件下結殼熱阻測試的實現方法。
1.環境溫度設置。為了更好地模擬工況條件,實驗過程直接在實驗室環境中進行,同時記錄測試時刻環境溫度的大小。
2.施加恒定功率。對IGBT模塊加恒定電流30A,因發生結溫分離點時刻約為數ms,故對模塊柵極加+15V脈沖信號,作用時間1s。經過實測和推算,這時產熱功率達到了52.6W。
3.設置不同散熱系數。由于2次測量需要給模塊設置不同的散熱系數,所以實驗過程中,第1次測量時,不做任何散熱處理,第2次測量時給模塊進行風冷。
4.結溫采樣。利用溫度信號解調器能夠對光纖探頭收集到的光信號進行處理并發送至PC機,PC機能夠對其進行曲線擬合和其他處理。在實驗中,結溫采樣頻率由計算機設定為9600Hz,也就是說溫度值每s可采集9600個,每0.1ms取樣一次。實測IGBT模塊在加載過程中的環境溫度Ta等于19.8°C。
3、 快速計算實驗條件結果及分析
嚴格按照以上實驗室條件進行測試,2次實驗采集的結溫點如圖7所示。
由圖7及采集點數據分析可知,2次測量結溫分離點時刻結溫為TJ(tp)=28.6℃。根據實驗條件可知,Ta=19.8℃,P=52.6W,根據式(2)求得模塊的結殼熱阻為RJC=0.1673℃/W。
經比對試驗計算結果表明:采用結溫分離點法進行模塊結殼熱阻的計算具有更高的準確度。同時實驗過程所需要的時間較少,不需要等模塊達到熱穩態就可以達到快速測量的目的。
通過分析試驗過程,總結發現在工況條件下使用該方法也存在一些不足:
1.工況條件下的IGBT模塊都有封裝結構,無法直接測量芯片結溫;
2.該測試方法需要在不同對流系數下進行2次測量,第1次結束后需等待IGBT模塊冷卻到環境溫度才可進行下一次測量;
3.工況下IGBT模塊均用于組裝散熱器,拆下散熱器或者更改散熱器和銅底板之間導熱硅脂厚度時工作較為煩瑣且影響IGBT模塊正常運行。
通過本文的分析可知,該IGBT模塊結殼溫度快速計算法具有以下優點:
1.無需測量模塊的殼溫,消除了測量IGBT 殼溫時因選取節點的隨機性而引入的計算誤差;
2.測量誤差較小;IGBT模塊芯片各部分溫度分布相差不大,因此測量點選擇的隨機性在計算熱阻時幾乎沒有影響,環境溫度及所加恒定功率均能在工況條件下測得精確;
3.測量周期短,由于熱量由模塊芯片向銅基板底面轉移的時間為10-3s量級,所以對IGBT模塊恒功率P施加所需的時間很短,收集一條結溫變化曲線只需幾個s即可完成。
結論
該文為尋求一種熱阻快速計算新方法,給出一種通過得到不同散熱情況下結溫變化曲線上分離點的IGBT模塊結殼熱阻解算方法。設計了一種在工況條件下用此方法解決IGBT模塊結殼熱阻問題的實施方法及具體試驗步驟,最后給出了仿真分析和試驗分析的結果,采用這種方法都能迅速,精確地得到IGBT模塊結殼熱阻。
總結知該方法具有計算誤差小、測量周期短的優點,可以實現準確、快速測量模塊結殼熱阻的要求。
-
IGBT
+關注
關注
1269文章
3833瀏覽量
250061 -
熱阻
+關注
關注
1文章
108瀏覽量
16513
發布評論請先 登錄
相關推薦
功率器件熱設計基礎知識
Simcenter Micred T3STER瞬態熱阻測試儀
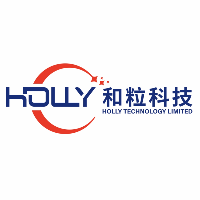
ADS58C20熱阻有頂面(9.3度/W)和底面(0.5度/W),請問一下折算為一面的熱阻怎么計算?
功率器件熱設計基礎(八)——利用瞬態熱阻計算二極管浪涌電流
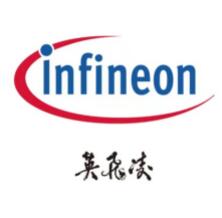
功率器件熱設計基礎(六)——瞬態熱測量
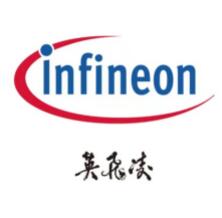
功率器件熱設計基礎(三)——功率半導體殼溫和散熱器溫度定義和測試方法
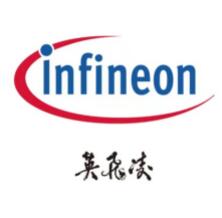
T3Ster瞬態熱測試方法與內容揭秘
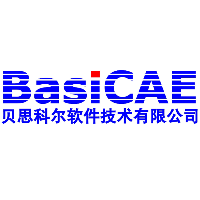
評論