在之前的文章中我們已經對凍干工藝有了一定的認識,并且完成了凍干工藝的整個步驟,接下來將介紹凍干的過程監測和驗證,給出您關于工藝設備選擇的建議以及整個凍干過程中需要考慮的事項。
凍干過程監測和驗證
為了確保高質量和最佳生產成本,我們使用樣品傳感器密切監測這一過程。在每次運行期間,每個擱板上的樣品都配備了記錄數據的溫度傳感器。有趣的地方是高溫條件可能導致樣品熔化的地方。每個擱板上通常至少有一個樣品配有溫度傳感器,但每個擱板上可能有多達5個樣品,放置在每個角落和中心。通常只有在流程優化時才需要實時數據,而批量記錄和驗證則不需要實時數據。在線數據可以通過使用有線熱電偶系統或無線數據記錄儀來獲得,其優點是易于定位且不改變腔室的完整性(無泄漏)。值得一提的是,凍干機的負載往往代表著極高的價值,這就是為什么真空泄漏或任何其他故障是不可容忍的。
測量西林瓶內產品溫度的推薦最佳做法是基于傳感器的類型、設計和尺寸。首先,與未受監測的西林瓶相比,任何放置在樣品中的傳感器都會給受監測的西林瓶帶來偏差,因為傳感器將/可以作為冰的成核位點。一些研究發現,對于特定產品,這種差異在受監測的西林瓶中可能高達5℃。由于冷凍速度較慢,它將產生更大的冰晶,這可能意味著更快的升華速度,這無法反映出未受監測西林瓶的確切狀況。
為了減少這種差異,傳感器應盡可能薄,因為這將有利于盡可能減少對樣品的影響,并有助于傳感器在西林瓶中的正確定位。這個位置位于幾何中心,幾乎接觸到西林瓶的底部。在初級干燥期間,這個位置將代表最后消失的冰,因此可能是未干燥產品的最熱的部分。如果傳感器一直放置在西林瓶的底部,測量的溫度可能會受到玻璃的影響,因此間接代表擱板溫度。如果傳感器在西林瓶內放置得太高,它將代表樣品的更多干燥部分。由于產品溫度和擱板溫度之間的比較經常被用來確定初級干燥的進度(當產品溫度等于擱板溫度時,標志著初級干燥結束),因此測量非常重要。
根據ISO 13408-3,每年一次或當維修/更換主要部件時,定期對凍干機進行重新驗證或鑒定,以通過以下測試確保其功能正常:
在無負載情況下對擱板溫度分布進行驗證,以驗證整個擱板溫度的均勻性(機器性能)。
擱板溫度分布與載荷的關系圖,以確定對樣品的影響。標準程序通常涉及具有溫度探頭的星形模式,溫度探頭被插入銅板的所有四個角以及每個擱板的中間。
凍干機驗證中涉及的進一步測試:
SIP(Steam-In-Place)溫度分布驗證,確保設備的適當現場滅菌。這就像凍干機是一臺滅菌器,而且證明無菌性的規范是相同的(EN 285 & EN17665 )。
真空泵測試,即測試真空系統的極限真空度和降溫時間。
溫度測試設備選擇
正如信息所示,理想的解決方案是一個無線數據記錄儀系統,帶有尺寸為30(非常薄)的裸端熱電偶儀表,以實現最佳產品監測。這個系統將結合兩個方面的優點——具有快速響應時間和小尺寸的熱電偶與無線數據記錄儀相結合——這種組合將消除冷凍干燥過程中與產品溫度測量相關的幾乎所有挑戰。通過使用數據記錄儀而非電纜系統,可以避免潛在的泄漏問題和耗時的電纜定位。由于冷凍干燥是一個相對較長的過程,需要幾個小時或幾天的時間,溫度低至-80℃,因此所使用的硬軟件必須可靠,并能夠長時間確保數據的完整性。
真空測試設備選擇
需要使用能在極低溫度下運行并配備高精度真空傳感器的無線數據記錄儀。尋找一個足夠精確的真空傳感器,為整個凍干機的流量測量提供數據,或者簡單地通過壓力上升測試(PRT)確定一次和二級循環的結束,以優化生產。
需要考慮的事項Things to Consider...01
溫度傳感器的設計
在實際的容器(西林瓶等)中測量產品的核心溫度是非常重要的,要盡可能地減少干擾。除了使用帶有熱電偶傳感器的無線數據記錄儀,使用帶有配件和固定裝置的特殊柔性PTFE傳感器來準確測量溫度也是可行的。PTFE電纜應該很細(直徑最大為1.8mm),并且提供專為凍干機設計的特殊瓶塞--Lyo瓶塞,這有助于模擬實際加工條件。同時,該設計確保將傳感器精確地安裝在西林瓶內的熱點處,熱點通常位于離西林瓶底部1到2mm處。只有柔性PTFE或熱電偶傳感器才能準確模擬實際過程。將不銹鋼傳感器插入西林瓶中,不會提供大量的熱傳導。
02
過程持續時間長
應要求數據記錄儀的電池壽命在低溫下能持續很長時間。當配備單傳感器時,每塊電池應能提供2-3,000個小時的工作時間,而配備雙傳感器時,工作時間則稍短。電池應設計為能在極低的溫度條件下正常工作,并易于現場更換。記錄儀內存也很重要。當與單個傳感器一起使用時,要尋找至少具有60-120.000個數據點和非易失性存儲器的存儲器容量。這意味著
以1秒采樣率運行16-32小時。
以5秒采樣率運行80-160小時。
以25秒采樣率運行400-800小時。
這保證了整個周期的無故障驗證。
03
實時數據選項
凍干機驗證通常要求每個擱板5個測量點——所有四個角以及中心——而批次控制可能要求每個擱板最多1個測量點,用于產品溫度批量控制。
當使用實時數據選項操作時,射頻發射器(SKY模塊)被安裝在記錄儀上。它是由同一個接收器(接入點)同時處理,數據通過專有的傳輸協議“流式傳輸”到軟件。數據記錄儀保留數據的 “安全副本”,直到它被發送到軟件上。
在開放空間具有高達100m的傳輸范圍是最理想的,前提是它能保證在封閉的室內(如凍干機)至少有15m的傳輸范圍。這意味著接收器可以放置在距離數據記錄儀15m的地方。如果凍干機非常大且長度超過15m,則可以連接更多接入點。
04
數據分析、數據完整性和FDA合規性
操作軟件最好完全符合FDA 21 CFR11的要求。為達到最佳使用效果,應收集數據并保存在數據記錄儀的存儲器中,然后,如果在線運行,應將數據傳輸到軟件中。該軟件最好具有在本地PC(客戶端)或在服務器上供相互使用的選項。
該軟件包應包括所有需要的文檔,包括IQ/ OQ、審計跟蹤和電子簽名。
05
傳感器與擱板的接觸
凍干驗證過程中的主要挑戰之一是,在放置傳感器進行擱板Mapping時限制對擱板的污染,同時還要保持適當的擱板接觸。典型的方法是在將傳感器粘在擱板上時使用熱熔膠,或使用能承受超低溫的特殊膠帶。
為避免這些難以在大型腔室深處進行的操作,可使用由特級不銹鋼制成的特殊等溫塊。該系統可確保良好的擱板接觸,因為傳感器的尖端可以插入等溫塊并放置在擱板上。
06
傳感器互換性
驗證凍干機需要多個測量點,因此為了避免將所有的數據記錄儀分配給同一個應用,獲取可廣泛應用的數據記錄儀系統可能是非常有幫助的。
如果系統允許溫度傳感器之間有完全的互換性,且溫度傳感器以及涵蓋其他測量參數(如真空、濕度、二氧化碳、電導率或壓力)的傳感器之間可以完全互換,則可以提供更具成本效益的解決方案。
07
校準
使用同一軟件進行手動、半自動和全自動校準的可能性,以及能夠使用任何可用的油槽/干井,將是非常有益的。溫度標準/參考儀器也應具有與軟件通信的能力。與數據記錄儀一起使用的傳感器通常由Pt1000熱電阻元件組成。在較長的時間內具有高度穩定性。由于這種穩定性,事前和事后的校準則并不一定要進行。
08
定期在線監測流程
無線數據記錄系統還可用于在生產過程中定期監測西林瓶的熱點溫度,以確保生產過程的安全。因此,軟件應考慮預定義的報警條件,如果溫度超過或低于預先設定的限制,則會向軟件和操作員的電子郵件地址發出報警。這些類型的安全警報有助于確保采取必要的措施,以避免損失。
結論CONCLUSION
虹科Ellab是全球領先的制藥、醫療、食品和其他行業完整熱驗證解決方案制造商。我們提供高精度的無線數據記錄儀和熱電偶系統,以進行可靠的驗證。
對于冷凍干燥(凍干),我們推薦可在極端條件下運行的HK-TrackSense Pro X/XL無線數據記錄儀。該記錄儀提供獨特的可互換傳感器系統,便于使用高性能的壓力、真空和溫度傳感器,甚至還有用于產品溫度測量的微型熱電偶。作為一個選項,我們建議使用SKY模塊進行實時數據通信。
加上直觀且符合FDA 21 CFR 11要求的HK-ValSuite數據分析和記錄軟件,以及一系列配件,使得整個解決方案成為冷凍干燥的獨特解決方案。
-
敏感元件
+關注
關注
1文章
87瀏覽量
15922 -
凍干機
+關注
關注
0文章
16瀏覽量
6187
發布評論請先 登錄
相關推薦
虹科電子12月事件回顧
虹科培訓 | 重磅來襲!波形分析課程全面上線!
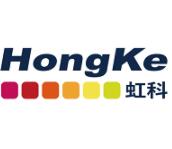
虹科活動回顧 | 波形診斷開放日-上海站圓滿落幕!
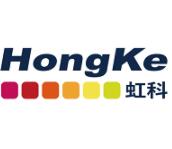
Aigtek亮相第十八屆全國壓電和聲波理論及器件應用研討會!
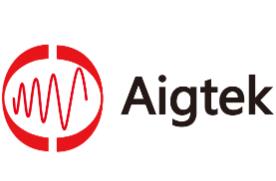
虹科培訓 | 重磅升級!全新模式月底開班,你想學的都在這里!
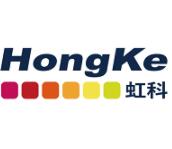
虹科應用 為什么虹科PCAN方案能成為石油工程通訊的首選?
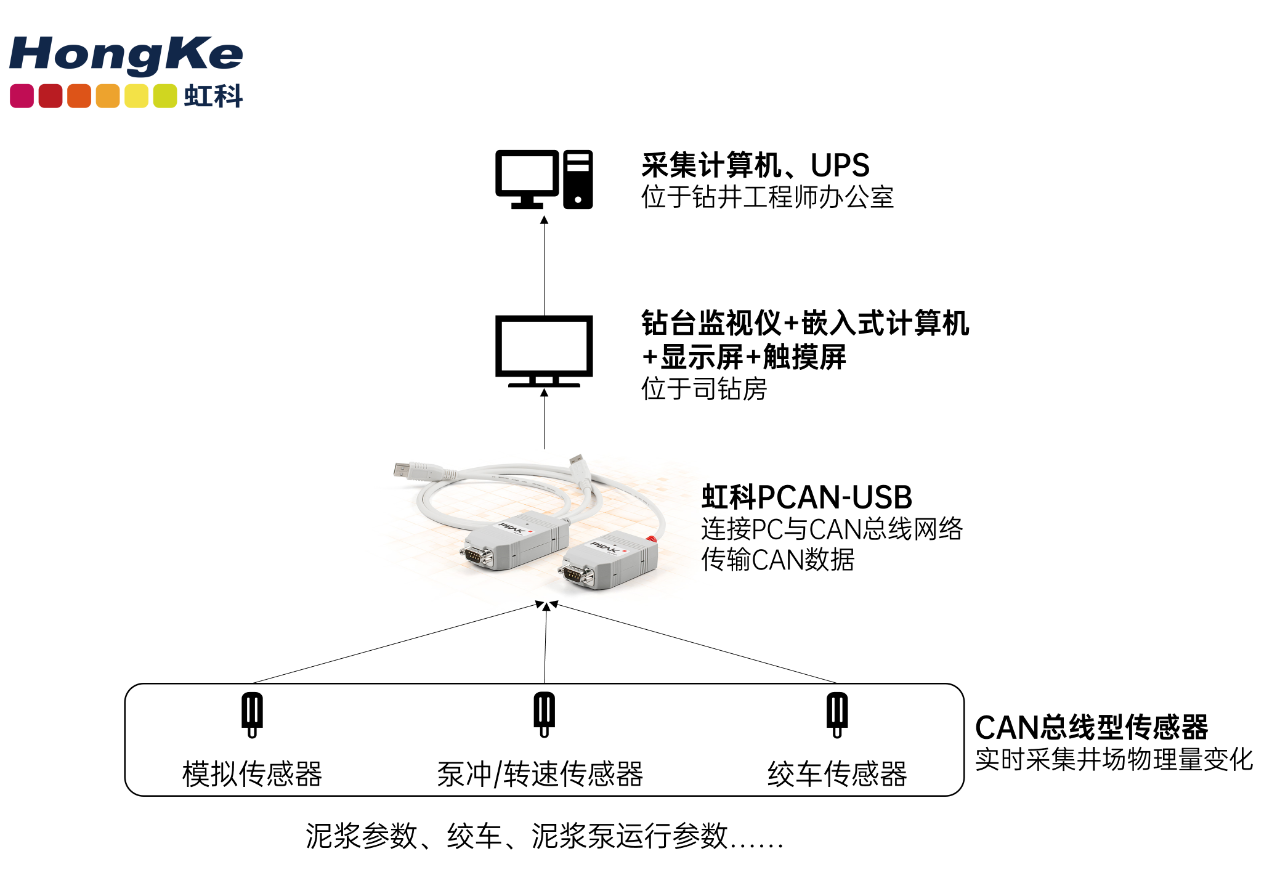
高清視界,盡在掌握——深度解析變焦機芯模組技術
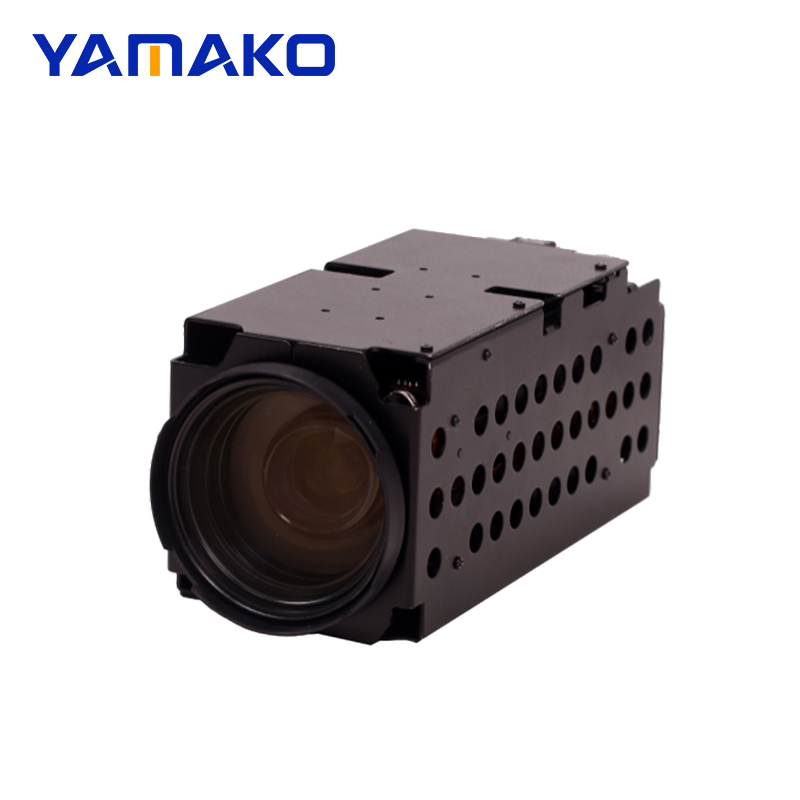
bq2750x系列中的Impedance Track?電池電量監測算法的理論及實現
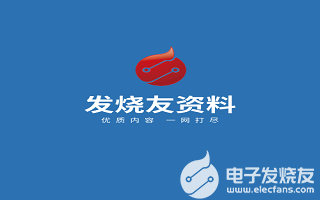
虹科干貨 輕松掌握PCAN-Explorer 6,dll調用一文打盡!
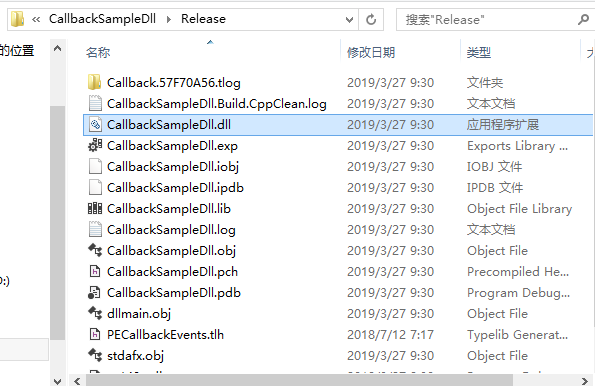
虹科方案 領航智能交通革新:虹科PEAK智行定位車控系統Demo版亮相
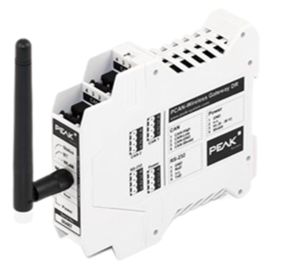
虹科應用 當CANoe不是唯一選擇:發現虹科PCAN-Explorer 6
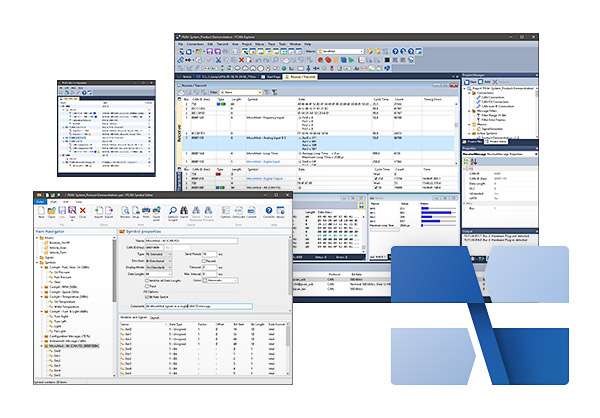
虹科案例|為什么PCAN MicroMod FD是數模信號轉換的首選方案?
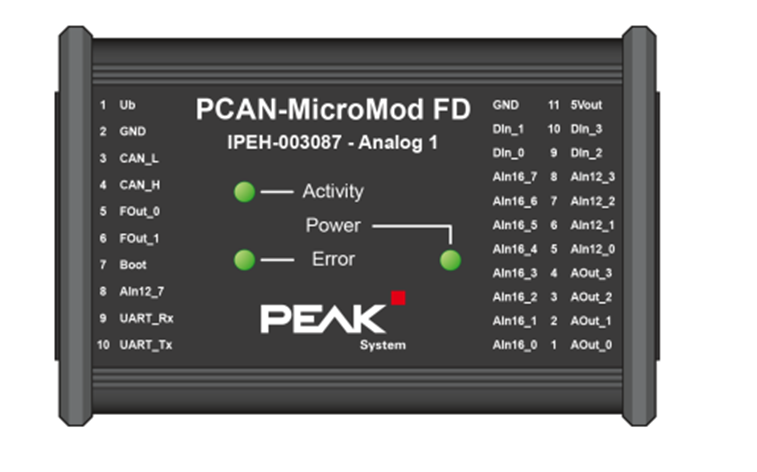
虹科干貨丨輕松掌握PCAN-Explorer 6,dll調用一文打盡!
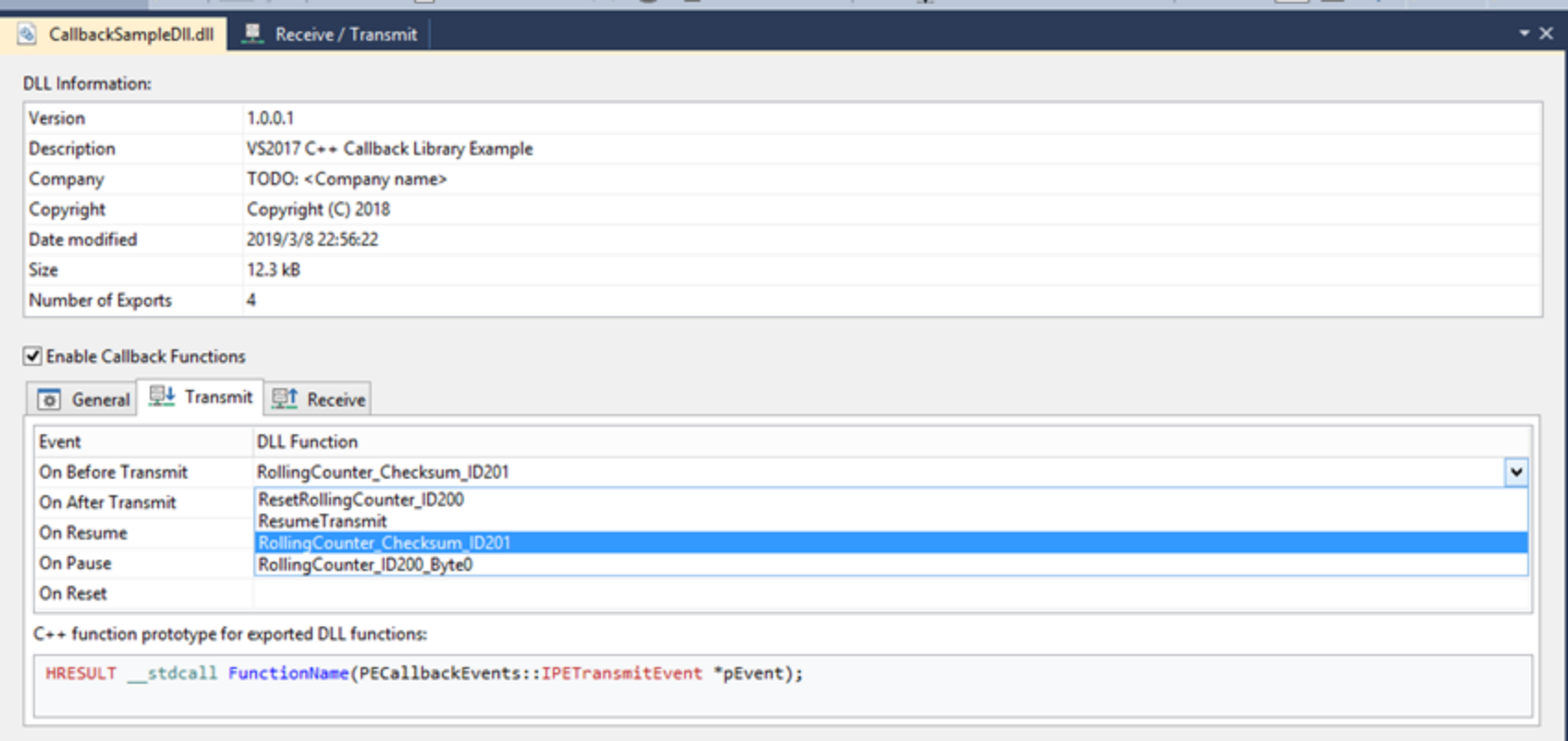
符合醫藥行業規范的液氮罐運輸和存儲溫度監測解決方案
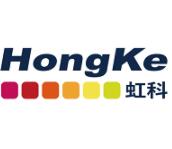
評論