2011年末頒布的歐6排放法規明確了未來幾年的需求框架。6.0×1011 km-1的顆粒數限值對直噴汽油機來說是真正的挑戰。通過可視化單缸發動機的研究,討論顆粒形成的因果關系,這可以為降低顆粒排放提出系統需求及功能定義。在1款歐5汽油機上進行的可再現性研究成功降低了發動機的原始排放,為噴油器中央布置的汽油機達到歐6顆粒數限值確定了方向。
近年來,汽油機呈現直噴化趨勢,但還必須面對顆粒排放法規限值日益收緊的態勢。在歐洲,即將實施的歐6排放法規在顆粒排放質量限值的基礎上,增加了顆粒數限值規定。本文將針對顆粒排放問題,就相關排放法規、顆粒生成原因分析,以及為實現歐6目標的直噴汽油機燃油噴射系統相應技術對策及評價結果等方面進行討論。
圖1 歐6顆粒數限值實施步驟
1 歐6排放法規的顆粒數限值
發動機排出的顆粒會對人類健康和大氣環境造成不利影響,因此,各國正在加強對粒徑100 nm以下顆粒排放的限制。2011年末,歐6排放法規將汽油機的顆粒數限值規定為6.0×1011 km-1,對直噴汽油機而言,這一限值是非常苛刻的。如圖1所示,上述排放限值將按照歐6b、歐6c的順序階段性地實施。另外,研究人員對在現有新歐洲行駛循環(NEDC)的基礎上增加實際行駛工況排放(RDE)也進行探討,但因為沒有限定詳細的條件,在現階段還無法開展具體的研究工作。在歐6之后,預計將在2020年,以全球統一輕型車測試循環(WLTC)為基礎,制定相應的法規。本文主要關注達到歐6最終顆粒數限值(6.0×1011 km-1)的技術途徑。
2 汽油機排放顆粒的生成要因
要減少汽油機的顆粒排放,就必須了解顆粒的生成過程。圖2是以柴油機為對象進行調查的結果,揭示了生成碳煙顆粒的氣體環境條件。由圖2可知,高溫與過濃混合氣是促進生成碳煙顆粒的要因。由于均質預混合汽油機在理論上不存在類似的過濃狀態,因此認為,汽油機中的碳煙生成與缸內燃油附著引起的局部過濃混合氣有關。
圖2 生成碳煙顆粒的氣體環境條件
圖3示出了直噴汽油機燃燒室內可能生成碳煙的燃油附著區域。除了由于早期噴射而有明顯燃油附著的活塞頂面(圖3①)外,還有因進氣門及進氣門座上部的噴霧沖擊和擴散引起的燃燒室頂部燃油附著(圖3②),因噴油引起的噴嘴端部燃油附著(圖3③),以及經由氣缸壁面油膜的活塞環岸處燃油附著(圖3④)。
圖3 汽油機中生成碳煙顆粒的潛在區域
上述燃油附著及碳煙生成情況可以通過圖4所示可視化單缸發動機的缸內攝影圖像、溫度曲線及放熱率曲線來加以證實。為滿足燃油耗方面的要求,汽油機的噴油定時被提前至340°CA BTDC,因此,在20°CA ATDC燃燒基本結束之后,活塞頂面仍然會殘留少量附著燃油。此時的氧濃度低于1%,計算所得的平均燃氣溫度約為2 000 K,這一條件與該部位燃油蒸發生成碳煙的條件基本一致。為此,在燃油附著處附近,可觀察到因放熱引起的發光現象。
圖4 基于曲軸轉角的燃燒過程及碳煙生成
生成碳煙的另一個原因是混合氣不均導致的局部混合氣過濃(圖3⑤)。新鮮空氣與燃油的混合不充分導致燃燒時的混合氣存在過濃區域,這也可能是導致生成碳煙顆粒的原因之一。
為了驗證上述理論,對與顆粒有關的各項參數進行研究。圖5為噴油定時對顆粒數變化趨勢的影響。如前文所述,噴油定時與燃油附著密切相關。從降低顆粒數的角度來看,為了避免活塞上的燃油附著,噴油定時應盡量提前。
圖5 顆粒數與噴油始點的關系
燃油噴射壓力是影響噴油霧化和蒸發的重要參數。圖6表示燃油壓力和油霧粒徑的關系,圖7所示燃油壓力與顆粒數的關系顯示出與圖6相似的趨勢,這說明提高噴油壓力有利于降低顆粒數。
圖6 通過提高燃油壓力降低油霧粒徑
圖7 通過提高燃油壓力降低顆粒數
3 滿足歐5排放法規的顆粒數水平
由于降低顆粒排放并不是車輛滿足歐5排放法規的重點,所以法規規定的顆粒數限值并不是能達到的最低值。但是,車輛的檢測值與作為課題的運行條件幾乎相同。圖8是歐5認證車輛在NEDC工況下進行顆粒數測量的結果。冷態運轉時催化轉化器預熱過程中排放的顆粒數較高,這是因為壁面附著的燃油蒸發緩慢,并經由前文所述過程生成碳煙顆粒。因此,關鍵是要盡量減少冷機時壁面附著的燃油。另外,車輛加速或高速行駛(高負荷)時的顆粒數也有明顯增加。因此,著重降低這些運行條件下的排放顆粒數會取得較好的效果。
圖8 NEDC工況下現有標準車輛的累計排放顆粒數
4 系統方法研究與各種運轉工況下的評價
如前文所述,生成顆粒的主要原因是燃燒室內附著燃油及混合氣的不均勻性。因此,本次研究采用以下技術對策:(1)改善噴油霧化,降低貫穿度;(2)優化各油束的噴射方向及噴油量分配;(3)提高微小噴油量階段的噴油精度;(4)優化靜態流量;(5)在整個運轉工況范圍內優化匹配。
4.1 激光加工噴油器噴孔
傳統的噴油器噴孔加工采用放電加工工藝,這種方法具有一定的實用優勢及可靠性,但在加工自由度及工件表面品質方面存在一定限制。為此,研究人員開發了激光加工工藝,并取得良好效果。相比放電加工工藝,激光加工工藝可以改善工件表面的精度,同時,可將噴孔入口的端面形狀加工得更為精確、整齊(圖9)。
圖9 分別由放電加工工藝和激光加工工藝制成的噴孔入口邊緣形狀
噴孔入口邊緣形狀更為精確可以使燃油在流入噴孔時形成強烈的紊流,由此在每個油束中產生劇烈破碎作用,從而降低貫穿度。圖10為相同形狀的噴嘴經放電加工和激光加工后的油束比較,可以發現,經激光加工后,油束角度更大。
圖10 分別經放電加工和激光加工工藝制成的噴孔油束形狀
另外,采用激光加工工藝,還可以加工出不同直徑的噴孔,從而實現燃燒室內燃油噴霧的自由分配。圖11為噴油器側置的直噴汽油機噴霧實例,采用這一型式的噴油器,可以實現壁面燃油附著量及混合氣均勻性的優化。
圖11 不同直徑的噴孔產生的噴霧形狀
4.2 微小噴油量階段的噴油量控制
要將降低貫穿度所必需的燃油量噴射到燃燒室內正確的位置,就必須在微小噴油量階段實現精準的噴射。在通電時間較短的運行區域,噴油器針閥在到達全行程前就要關閉,其運動軌跡呈放射線形狀。與全行程區域不同,在這一區域,即使是相同結構的噴油器,其不同個體之間針閥的運動也會有很大差異,而細微的制造偏差會影響針閥的開啟時間。為此,開發了基于發動機電控單元(ECU)軟件的閉環控制方法:通過檢測各噴嘴的開閉時刻,控制針閥開啟時間,使其接近平均值。圖12為實施閉環控制后的針閥升程改善結果。通過采用這種方法,可以抑制整個使用壽命期內針閥動作的偏差。
圖12 有無閉環控制的噴油器針閥升程曲線
4.3 發動機起動和催化轉化器預熱
采用激光加工噴孔的噴油器和微小噴油量階段的閉環控制方法,對噴油器中央布置的直噴汽油機的起動性能及催化轉化器預熱性能進行研究。圖13為歐5標準的汽油機排放顆粒數的檢測結果。在起動后約30 s的時間內,發動機是在催化轉化器預熱模式下運轉的。這里所說的“催化轉化器預熱模式”,是指為實現催化轉化器的快速升溫,進行多次噴射,第2次噴射在臨近點火前進行,以確保燃燒穩定性,并盡可能延遲點火定時。
圖13 歐5汽油機在起動及催化轉化器預熱階段的顆粒數
接著,研究降低顆粒數的方法。首先,將起動時的噴油定時從壓縮行程移至進氣行程。另外,為了改善混合氣的形成,將燃燒壓力設定為盡早達到系統壓力上限的20 MPa。由于催化轉化器預熱的第2次噴射接近活塞上止點,會造成燃油附著,同時,由于到點火的時間較短,導致氣化不充分,這些都成為生成顆粒的主要原因。圖14為噴油器中央布置的直噴汽油機在改變第2次噴射的噴油量時顆粒數的變化趨勢。在這一噴油區間,為確保噴油量的精度,以及在產品使用壽命期內的噴油精度,使用閉環控制方法的噴射脈沖控制是較為理想的。
圖14 噴油器中央布置的直噴汽油機在催化轉化器預熱過程中第2次噴射的噴油量與排放顆粒數的關系
采用上述對策后,發動機起動與催化轉化器預熱過程的排放顆粒數如圖15所示,在此基礎上,再采用激光噴孔加工工藝對噴霧進行優化,并配合包括閉環控制在內的噴油優化策略,最終結果如圖16所示。可以發現,因為采用閉環控制的優化策略及噴霧優化的效果,有效降低了排放顆粒數。
圖15 實施包括閉環控制在內的優化策略后,在發動機起動及催化轉化器預熱過程中的排放顆粒數
圖16 采用激光加工噴孔的噴油器、優化的噴霧設計,以及包括閉環控制在內的優化標定的汽油機在起動及催化轉化器預熱過程中的排放顆粒數
4.4 預熱過程中的加速及高負荷運轉階段
即使在催化轉化器預熱之后,也存在數量不可忽視的顆粒。在嘗試推遲噴油定時的策略后,發現會引起混合氣均勻性惡化,并導致燃油經濟性變差,所以,嘗試通過優化噴霧來解決問題。圖17為匹配歐5標準車輛的量產噴油器與經優化的噴油器的比較結果。由結果可知,經優化后,幾乎所有噴油時刻的排放顆粒數都有所降低,某些條件下的改善效果甚至達到10倍以上。其他改善方法還包括多次噴射,這可以降低貫穿度及進氣門的燃油附著,但也需要注意混合氣均勻性惡化的問題。
圖17 分別采用歐5量產噴油器與優化噴油器的強制冷卻發動機排放顆粒數比較(發動機轉速1 500 r/min,平均有效壓力0.7 MPa)
5 系統優化方法的導入及對車輛的評價
下文將介紹對實際車輛的評價結果。試驗車質量為1 800 kg,采用噴油器中央布置的渦輪增壓汽油機。首先,采用包括閉環控制在內的降低顆粒數的優化策略,達到3×1012 km-1的目標,顆粒數被降低到歐6b階段限值的1/2。接著,應用前文介紹的各種優化策略后,排放值達到6.4×1012 km-1。然后,再進一步增加燃油壓力,特別針對預熱和加速過程,使顆粒數達到3×1011 km-1,完全達到歐6c最終限值的水平(圖18)。
圖18 采用優化的噴油器,以及包括閉環控制在內的優化噴油策略后,車輛在NEDC工況下的顆粒數水平
上述系統化方法的效果同樣也在幾臺噴油器側置的汽油機和車輛上得到確認,比較結果如圖19所示。由于燃燒方式不同,同樣策略的效果也會有所不同,需要分別對其進行研究和評價。
圖19 測試燃燒過程的評價矩陣
6 對替代方案的考察
在每臺發動機固有的優化措施基礎上,還研究了降低排放顆粒數的其他方法。采用缸內直噴與進氣道噴射相結合的技術,也可以降低顆粒數,但必須考慮到噴油系統成本增加、優化及診斷開發周期延長,以及燃油蒸發排放等方面的影響。
如前文所述,提高燃油壓力是有效的方法。目前量產系統的壓力上限是20 MPa,今后將有望進一步提高壓力。圖20為通過外部加壓的方式,在2.0 L渦輪增壓發動機上得到的試驗結果。在通過提高壓力獲得的顆粒數降低效果中,包括一小部分配合噴油量降低噴嘴靜態流量的效果。由試驗結果可知,當燃油壓力達到30 MPa以上,顆粒數降低效果將達到極限。另外,提高燃油壓力也會造成高壓燃油泵的驅動摩擦損失增加,從而導致燃油耗增加。
圖20 顆粒數隨燃油壓力的變化
顆粒捕集器已在柴油機上獲得實際應用。將這一技術用于汽油機時,由于與柴油機相比,發動機外部的排放水平較低,因此必須針對汽油機調整捕集效率,這可以抑制對發動機性能的影響,但需要從再生控制、診斷,以及成本方面確認這些影響。
7 結語
(1)歐6排放法規將導入針對直噴汽油機的顆粒數限值,為達到將在2017年實施的歐6c顆粒數最終限值(6.0×1011 km-1),對現有的直噴汽油機必須實施相應的改進措施。
(2)利用可視化單缸發動機進行試驗,分析顆粒的生成原因,確認針對燃油系統要求的方向性。
(3)將以下優化策略用于噴油器中央布置的汽油機,并證實其能夠滿足歐6c最終限值的要求:改變噴嘴噴孔的加工工藝,促進燃油霧化,降低貫穿度;優化各噴束的油量分配及噴射方向;在極小脈沖區域引入閉環控制方法,降低噴油量的波動;設定20 MPa的高油壓,改變噴油定時。
(4)作為替代方案,可以應用缸內直噴與進氣道噴射相結合的系統,并進一步提高燃油壓力,或采用汽油機顆粒捕集器等技術。這些方法能有效降低顆粒數,但需要考慮對發動機性能及成本方面的影響。
-
發動機
+關注
關注
33文章
2498瀏覽量
69711 -
汽油機
+關注
關注
0文章
58瀏覽量
11573 -
汽車噴油器
+關注
關注
0文章
9瀏覽量
6296
發布評論請先 登錄
相關推薦
汽油機換擋油門控制電路設計
用光學法對汽油機燃燒循環變動的測量和評價
基于DSP的汽油機點火參數自動測試系統
電感儲能式汽油機點火器總成技術條件
運用CPLD器件和AT89C52實現汽油機點火參數測量儀的設計
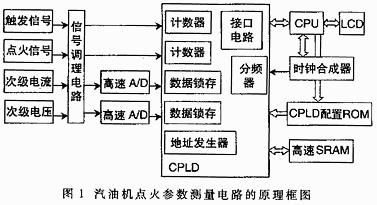
評論